Methodology
The tool is intended to provide high level guidance on the potential effect of design choices on embodied carbon particularly suitable for early to schematic building designs. It uses building archetypes and explores variations in design on that archetype.
The data behind the tool – visible in the table below the graphic results display – was generated with parametric LCA modelling. In other words, for each archetype, all realistic combinations of the selected design variables were modelled in LCA software. The embodied carbon results from each run are captured in the table. These pre-calculated results are accessed by the tool when users interactively engage with the tool.
Selection of building archetypes
A total of eight building archetypes were modelled:
- High-rise residential
- Mid-rise residential
- Stacked townhouses
- Single family home
- High-rise office
- Mid-rise office
- Strip mall
- Elementary school
These were selected in consultation with stakeholders. The designs selected for each archetype are fictional but are believed to be representative of what might be expected for these archetypes in these regions.
Selection of design variables
Variable types and iterations explored were developed with the intent of achieving realistic possible changes and/or changes that could result in significant change in embodied impact. These were selected based on review of existing building designs, using our knowledge of the building industry and embodied impacts, and with the input of others in the LCA and design industries.
See Tables 1 to 8 for details on each archetype:
High-Rise Commercial | Options |
---|---|
Occupancy | Office with retail on ground floor |
Floor plate | 40 m x 40 m |
No of stories | 40 |
Floor to floor height | 3 m, 4 m |
Foundation | Reinforced concrete footings, below grade concrete walls and slab |
Structural system | Reinforced concrete Steel Encapsulated mass timber glulam |
Floor system | Reinforced concrete Hollow core concrete Composite steel deck Mass timber (CLT) with concrete topping |
Exterior wall system | Aluminum curtain wall system Concrete block wall assemblies Mass timber (CLT) Steel stud infill wall assemblies Unitized aluminum insulated walls Unitized steel insulated walls |
Cladding | Brick Metal panel Precast concrete Single panel glass panel Stone |
Wall insulation | 152 mm Fiberglass batt (between studs only) 102 mm, 152 mm Mineral wool insulation 102 mm, 152 mm Polyisocyanurate (Polyiso) |
Roof insulation | 203 mm Mineral wool insulation 203 mm Polyisocyanurate (Polyiso) |
Roof Membrane | 2-ply Modified bitumen SBS Built-up roof PVC |
Glazing | Double glazed low-e argon, Triple glazed double low-e argon |
Window frame | Aluminum punched windows Aluminum curtain wall |
Window to wall ratio | 40%, 60%, 80% |
Underground parking | None (street) 2 levels 4 levels 6 levels |
SCMs in concrete | 0%, 20%, 30%, 40% |
Mid-Rise Commercial | Options |
---|---|
Occupancy | Office with retail on ground floor |
Floor plate | 40 m x 40 m |
No of stories | 10 |
Floor to floor height | 3 m, 4 m |
Foundation | Reinforced concrete footings, below grade concrete walls and slab |
Structural system | Reinforced concrete Steel Encapsulated mass timber glulam |
Floor system | Reinforced concrete Hollow core concrete Composite steel deck Mass timber (CLT) with concrete topping |
Exterior wall system | Aluminum curtain wall system Concrete block wall assemblies Mass timber (CLT) Precast insulated sandwich panel Steel stud infill wall assemblies Unitized aluminum insulated walls Unitized steel insulated walls |
Cladding | Brick Metal panel Precast concrete Precast insulated sandwich panel Single panel glass panel Stone |
Wall insulation | 152 mm Fiberglass batt (between studs only) 102 mm, 152 mm Expanded polystyrene (EPS) 102 mm, 152 mm Mineral wool insulation 102 mm, 152 mm Polyisocyanurate (Polyiso) |
Roof insulation | 203 mm Mineral wool insulation 203 mm Polyisocyanurate (Polyiso) |
Roof Membrane | 2-ply Modified bitumen SBS Built-up roof PVC |
Glazing | Double glazed low-e argon Triple glazed double low-e argon |
Window frame | Aluminum curtain wall Aluminum punched windows |
Window to wall ratio | 40%, 60%, 80% |
Underground parking | None (street) 2 levels |
SCMs in concrete | 0%, 20%, 30%, 40% |
Strip Mall | Options |
---|---|
Occupancy | Retail |
Floor plate | 17.5 m x 6.5 m |
No of stories | 2 above grade + basement |
Floor to floor height | 3 m |
Foundation | Reinforced concrete footings, below grade concrete walls and slab |
Structural system | Reinforced concrete Steel Mass timber glulam |
Floor system | Reinforced concrete Hollow core concrete Composite steel deck Mass timber (CLT) with concrete topping |
Exterior wall system | Concrete block wall assemblies Insulated concrete forms (ICF) Mass timber (CLT) Precast concrete Precast insulated sandwich panel Steel stud infill wall assemblies |
Cladding | Brick Exterior insulation and finish system (EIFS) Metal panel Precast concrete Precast insulated sandwich panel Stone |
Wall insulation | 152 mm Fiberglass batt (between studs only) 102 mm, 152 mm Expanded polystyrene (EPS) 102 mm, 152 mm Extruded polystyrene (XPS) 102 mm, 152 mm Mineral wool insulation 102 mm, 152 mm Polyisocyanurate (Polyiso) 102 mm, 152 mm Spray applied polyurethane foam (Spray Foam) |
Roof insulation | 203 mm Expanded polystyrene (EPS) 203 mm Extruded polystyrene (XPS) 203 mm Mineral wool insulation 203 mm Polyisocyanurate (Polyiso) |
Roof Membrane | 2-ply Modified bitumen SBS Built-up roof PVC TPO |
Glazing | Double glazed low-e argon Triple glazed double low-e argon |
Window frame | Aluminum punched windows Fiberglass punched windows |
Window to wall ratio | 40%, 60% |
Underground parking | None (street, surface lot) |
SCMs in concrete | 0%, 20%, 30%, 40% |
Elementary School | Options |
---|---|
Occupancy | Institutional |
Floor plate | 75 m x 25 m |
No of stories | 2 |
Floor to floor height | 6.5 m |
Foundation | Reinforced concrete footings, below grade concrete walls and slab |
Structural system | Reinforced concrete Steel Mass timber glulam |
Floor system | Reinforced concrete Hollow core concrete Composite steel deck Mass timber (CLT) with concrete topping |
Exterior wall system | Concrete block wall assemblies Insulated concrete forms (ICF) Mass timber (CLT) Precast concrete Precast insulated sandwich panel Steel stud infill wall assemblies |
Cladding | Brick Exterior insulation and finish system (EIFS) Metal panel Precast concrete Precast insulated sandwich panel Single panel glass panel |
Wall insulation | 152 mm Fiberglass batt (between studs only) 102 mm, 152 mm Expanded polystyrene (EPS) 102 mm, 152 mm Mineral wool insulation 102 mm, 152 mm Polyisocyanurate (Polyiso) 102 mm, 152 mm Spray applied polyurethane foam (Spray Foam) |
Roof insulation | 203 mm Expanded polystyrene (EPS) 203 mm Extruded polystyrene (XPS) 203 mm Mineral wool insulation 203 mm Polyisocyanurate (Polyiso) |
Roof Membrane | 2-ply Modified bitumen SBS Built-up roof EPDM PVC |
Glazing | Double glazed low-e argon, Triple glazed double low-e argon |
Window frame | Aluminum storefront curtain wall Aluminum punched windows Fiberglass punched windows |
Window to wall ratio | 16%, 32% |
Underground parking | None (street, surface lot) |
SCMs in concrete | 0%, 20%, 30%, 40% |
High-Rise Residential | Options |
---|---|
Occupancy | Mixed use multi-unit residential with retail on ground floor |
Floor plate | 25 m x 25 m |
No of stories | 30 |
Floor to floor height | 3 m, 4 m |
Foundation | Reinforced concrete footings, below grade concrete walls and slab |
Structural system | Reinforced concrete Encapsulated mass timber glulam |
Floor system | Reinforced concrete Hollow core concrete Composite steel deck Mass timber (CLT) with concrete topping |
Exterior wall system | Aluminum curtain wall system Aluminum window wall system Concrete block wall assemblies Mass timber (CLT) Precast insulated sandwich panels Steel stud infill wall assemblies Unitized aluminum insulated walls Unitized steel insulated walls |
Cladding | Brick Exterior Insulation and Finish System (EIFS) Metal panel Precast concrete Precast insulated Sandwich Panel Single panel glass panel Stone |
Wall insulation | 152 mm Fiberglass batt (between studs only) 102 mm, 152 mm Expanded Polystyrene (EPS) 102 mm, 152 mm Mineral wool insulation 102 mm, 152 mm Polyisocyanurate |
Roof insulation | 203 mm Extruded polystyrene (XPS) 203 mm Mineral wool insulation 203 mm Polyisocyanurate (Polyiso) |
Roof Membrane | 2-ply Modified bitumen SBS PVC Built-up roof TPO |
Glazing | Double glazed low-e argon Triple glazed double low-e argon |
Window frame | Aluminum curtain wall Aluminum window wall Aluminum punched windows Fiberglass punched windows |
Window to wall ratio | 40%, 60% |
Underground parking | None (street), 2 levels 4 levels, 6 levels |
SCMs in concrete | 0%, 20%, 30%, 40% |
Mid-Rise Residential | Options |
---|---|
Occupancy | Mixed use multi-unit residential with retail on ground floor |
Floor plate | 75 m x 25 m |
No of stories | 6 |
Floor to floor height | 3 m |
Foundation | Reinforced concrete footings, below grade concrete walls and slab |
Structural system | Reinforced concrete Steel Load bearing wood frame walls Encapsulated mass timber glulam |
Floor system | Reinforced concrete Wood joists Wood I joists Mass timber (CLT) with concrete topping |
Exterior wall system | Aluminum window wall system Insulated concrete forms (ICF) Mass timber (CLT) Steel stud infill wall assemblies Wood stud infill wall assemblies |
Cladding | Brick Exterior Insulation and Finish System (EIFS) Fiber cement board Metal panel Vinyl siding |
Wall insulation | 152 mm Cellulose batt (between studs only) 152 mm Fiberglass batt (between studs only) 102 mm, 152 mm Expanded Polystyrene (EPS) 102 mm, 152 mm Extruded Polystyrene (XPS) 102 mm, 152 mm Mineral wool insulation 102 mm, 152 mm Polyisocyanurate (Polyiso) |
Roof insulation | 203 mm Expanded polystyrene (EPS) 203 mm Extruded polystyrene (XPS) 203 mm Mineral wool insulation 203 mm Polyisocyanurate (Polyiso) |
Roof Membrane | 2-ply Modified bitumen SBS PVC Built-up roof TPO |
Glazing | Double glazed low-e argon Triple glazed double low-e argon |
Window frame | Aluminum punched windows Fiberglass punched windows PVC vinyl punched windows |
Window to wall ratio | 40%, 60% |
Underground parking | None (street) 1 level |
SCMs in concrete | 0%, 20%, 30%, 40% |
Stacked Townhome | Options |
---|---|
Occupancy | Residential |
Floor plate | 12 m x 6 m |
No of stories | 3 |
Floor to floor height | 3 m |
Foundation | Reinforced concrete footings, below grade concrete walls and slab |
Structural system | Load bearing wood frame walls Mass timber glulam |
Floor system | Wood joists Wood I joists Mass timber (CLT) without concrete topping |
Exterior wall system | Insulated concrete forms (ICF) Mass timber (CLT) Steel stud infill wall assemblies Wood stud infill wall assemblies |
Cladding | Brick Exterior Insulation and Finish System (EIFS) Fiber cement board Metal panel Vinyl siding |
Wall insulation | 152 mm Cellulose batt (between studs only) 152 mm Fiberglass batt (between studs only) 152 mm Spray applied polyurethane foam (Spray Foam) (between studs only) 102 mm, 152 mm Expanded Polystyrene (EPS) 102 mm, 152 mm Extruded Polystyrene (XPS) 102 mm, 152 mm Mineral wool insulation 102 mm, 152 mm Polyisocyanurate (Polyiso) |
Roof insulation | 203 mm Expanded polystyrene (EPS) 203 mm Extruded polystyrene (XPS) 203 mm Mineral wool insulation 203 mm Polyisocyanurate (Polyiso) |
Roof Membrane | 2-ply Modified bitumen SBS PVC Built-up roof TPO |
Glazing | Double glazed low-e argon, Triple glazed double low-e argon |
Window frame | Aluminum punched windows Fiberglass punched windows PVC vinyl punched windows Wood punched windows |
Window to wall ratio | 10%, 25% |
Underground parking | None (street) |
SCMs in concrete | 0%, 20%, 30%, 40% |
Single Family Home | Options |
---|---|
Occupancy | Residential |
Floor plate | 10.1 m x 7.75 m |
No of stories | 2 above grade + basement |
Floor to floor height | 3 m |
Foundation | Reinforced concrete footings, below grade concrete walls and slab |
Structural system | Load bearing wood frame walls Steel |
Floor system | Wood joists Wood I joists Steel |
Exterior wall system | Insulated concrete forms (ICF) Steel stud infill wall assemblies Wood stud infill wall assemblies |
Cladding | Brick Exterior Insulation and Finish System (EIFS) Fiber cement board Metal panel Stucco Vinyl siding Wood |
Wall insulation | 152mm Cellulose batt (between studs only) 152 mm Fiberglass batt (between studs only) 102 mm, 152 mm Spray applied polyurethane foam (Spray Foam) (between studs only) 102mm, 152 mm Expanded Polystyrene (EPS) 102mm, 152mm Extruded Polystyrene (XPS) 102mm, 152 mm Mineral wool insulation 102mm, 152 mm Polyisocyanurate (Polyiso) |
Roof insulation | 152 mm Cellulose 152 mm Expanded polystyrene (EPS) 152 mm Extruded polystyrene (XPS) 152 mm Fiberglass batt 152 mm Mineral wool insulation 152 mm Polyisocyanurate (Polyiso) |
Roof Membrane | Asphalt shingles Metal |
Glazing | Double glazed low-e argon, Triple glazed double low-e argon |
Window frame | Aluminum punched windows Fiberglass punched windows PVC vinyl punched windows Wood punched windows |
Window to wall ratio | 10%, 25% |
Underground parking | None (street) Garage |
SCMs in concrete | 0%, 20%, 30%, 40% |
Building Model Scope
The LCA modelling focused on the building structure and above grade and below grade building envelope assemblies. The bills of materials were created using the Impact Estimator “assembly” method. The models included the following where applicable:
- Main structure including beams, columns, floor slabs, load bearing walls, shear walls foundation walls, and footings.
- Exterior walls and windows, including various wall types and systems, insulation, vapour and air barriers, cladding, window framing and glazing, roofing membrane.
- Parking garages including structure and membranes.
The models did not include ceiling or floor coverings, finish materials, paint, interior walls (other than interior load bearing walls for the mid-rise and single-family home wood-frame buildings), mechanical or electrical systems, or site components.
System Boundary
The system boundary for the LCA models included the product, construction, use and end of life stages excluding operational energy and water. This includes stages A1-A5, B1 to B4, and C1 to C4. Stages B5, B6, B7 and D were excluded. See Figure 1 for an illustration of life cycle stages included and excluded.
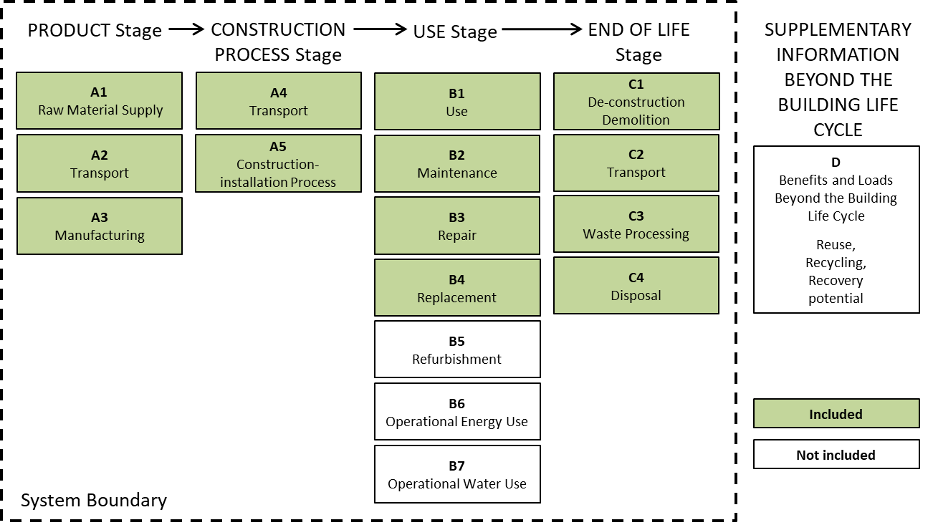
Data, assumptions, and results
The Athena Building Impact Estimator (Version 5.5.01) was used to model the impact of most of the various design iterations on embodied carbon (i.e., embodied global warming potential). The Impact Estimator generally follows the National Guidelines for Whole-building LCA and relevant standards (EN 15978 and ISO 21930).
GWP/m² results are provided in multiple ways:
- GWP with biogenic carbon is cradle-to-grave results including the carbon stored in organic materials (e.g. wood) which was derived from carbon dioxide removed from the atmosphere by the living plant. Including biogenic carbon gives a benefit to (i.e. reduces) GWP. Gross floor area is the entire area of the project. This GWP result is per the National Guidelines.
- GWP without biogenic carbon is the same as above but does not include the carbon stored in organic materials. This GWP result is per the CAGBC Zero Carbon Program.
- GWP A1-A5 is cradle-to-end-of-construction results without biogenic carbon. This GWP result is per the Toronto Green Standard.
- GWP Van is cradle-to-grave results without biogenic carbon and where the results include the parkade but the gross floor area does not. This GWP result is per the City of Vancouver embodied carbon policy.
For more information on the background material data and assumptions, see the Impact Estimator User Manual.
The Impact Estimator was used to estimate both material quantities and their embodied impacts. Exceptions and workarounds are presented below:
Structural Grid Spacing:
The structural designs of the archetype buildings were based on the Assembly Method in the Impact Estimator with standard assumptions for the grid spacing of the beams and columns. The structural grid spacing for concrete and steel structural systems were assumed to be the same but were reduced to approximately half for the mass timber design to reflect typical designs. All floors were considered to have a live load of 2.4 kPa.
The structural grid spacing for the archetypes are shown in Table 9.
Archetype | Structural Grid Spacing | ||
---|---|---|---|
Concrete and Steel | Mass Timber | Load Bearing Wood Frame | |
High-Rise MURB, High-Rise Commercial, Mid-Rise Commercial, and Elementary School | 8 m x 8 m | 3 m x 4 m | n/a |
Mid-Rise MURB | 8 m x 8 m | 3 m x 4 m | 3 m x 4 m |
Strip Mall | 6 m x 7.6 m | 3 m x 3.8 m | n/a |
Stacked Townhome | n/a | 3 m x 4 m | 3 m x 4 m |
Single Family Home | 3 m x 4 m (steel only) | n/a | 3 m x 4 m |
Encapsulation of mass timber structural components were considered for applicable archetypes based on local building code requirements. Two-layers of 12.7 mm Type X gypsum board were added around the exposed surfaces of the mass timber beams and columns following the Guide to Encapsulated Mass Timber Construction in the Ontario Building Code report published by the Canadian Wood Council in July 2022. As of 2024, encapsulation of mass timber structures are only required for buildings up to 12 storeys in Ontario and between 6 to 18 storeys in British Columbia.
Structural Columns:
In multi-storey buildings, structural columns support not only the floor immediately above, but also the loads of the column immediately above. As such, columns effectively support loads from all floors above, such that lower floor columns are typically larger than upper floor columns. While the software did not factor in the additive load on columns in taller buildings, the structures in the archetype buildings did by considering the total supported area of the floors above the column in the LCA models. The column sizes were assumed to only change every 10 floors, such that all the columns within a 10-storey section of the building would have the same size as the lowest level of that section (e.g. Level 10 columns have the same size as Level 1 columns). This decision was made based on a review of multiple real designs and our knowledge of the industry.
Concrete and Supplementary Cementitious Materials (SCMs):
35 MPa Portland Cement concrete was assumed for all cast-in-place concrete above and below grade structures for all archetype buildings.
SCMs created an issue as a change in SCMs could potentially impact many assemblies within a building. To resolve this issue, we compared the GWP of several different SCM ranges for several different concrete-based building assemblies. More specifically, we reviewed the following assemblies: Slab on grade, footings, beams and columns, concrete walls, and concrete in extra basic materials within the software. For each of these assemblies we compared 0, 20%, 30%, and 40% SCM contents. We found that changing from 0 to 20% SCM content resulted in a reduction in GWP by between 3.6 and 5.2% for the various assemblies. Similarly, changing from 0 to 30% SCM content resulted in a reduction in GWP by between 10.4 and 12.2% and changing from 0 to 40% SCM content resulted in a reduction in GWP by between 15.5 and 20.1%. For this tool, we used the average change of impacts for the different assemblies. More specifically, we applied factors to all concrete based assemblies to estimate the impact of different SCM contents as shown in Table 10.
SCM content | SCM factors from base case |
---|---|
0 | 1 |
20 | 0.96 |
30 | 0.89 |
40 | 0.82 |
Wood Frame Load Bearing Walls:
The software did not factor in the additive load on load bearing walls in multi-story buildings: load bearing walls support not only the floor immediately above, but also the load of any load bearing walls above it. This resulted in a significant underestimation of lower floor load bearing walls in the six-story design. To resolve this issue, the wood framing for the bottom three floors of the archetype was increased by an additional 25% to account for extra studs at window openings and interior partition walls. Note this was not considered a significant error in the stacked townhouse design as the additive effects are small and it would not be typical to change the stud spacing across the height of this type of building. These decisions were made based on a review of multiple real designs and our knowledge of the industry.
Mixed-Used Occupancy:
Archetypes that typically have mixed-used occupancy, with commercial on the ground floor and residential above, were addressed. For these archetype buildings, the level 1 structure was composed of reinforced concrete columns and floor with 100% glazed double glazed curtain wall system for the building envelope, similar to that of storefront glazing. The heights of the first level were also increased as listed in Table 11.
Archetype | Structure Type | Height | Building Envelope |
---|---|---|---|
High-Rise Commercial and Mid-Rise Commercial | Reinforced Concrete | 5.5 m | Double-Glazed Aluminum Curtain Wall with 100% Vision |
High-Rise MURB and Mid-Rise MURB | Reinforced Concrete | 4 m | Double-Glazed Aluminum Curtain Wall with 100% Vision |
Building Envelope Insulation:
The exterior wall insulation is divided into two parts: interior insulation and exterior insulation.
- Interior Insulation: refers to the insulation between studs in wood-frame and steel-frame walls.
- Exterior Insulation: refers to the insulation outboard of the back up wall framing and is often continuous
Cladding support systems such as brackets and girts were not considered as part of the exterior wall assemblies. As a result, the exterior insulation for the archetypes is considered to be continuous.
Typical insulation thicknesses were considered for the archetype buildings. Although different insulation types have different thermal conductivities, the insulation quantities were not adjusted to have the same thermal resistance since that will create atypical insulation thicknesses that are not available. Instead, all insulation types were set to predetermined thicknesses based on current building trends in 2024.
Project Team
The Stantec team (formerly Morrison Hershfield) involved in the development of the tool, and this document are:
- Mark Lucuik - Director of Sustainability
- Kalum Galle - Team Lead, Sustainability Specialist
- Ivan Lee - Building Science Engineer
Limitations
By nature, whole-building LCA results are uncertain and should be used as a guidepost and not an absolute. Although the archetype designs are believed to be typical for the regions, actual designs will vary. The further a real design strays from the archetype design the less reliable the results.
The LCA results are specific to the region presented. Actual results can vary significantly for other regions.
For project-specific results, a custom whole-building LCA is needed. Access free software tools at www.athenasmi.org.